Why jute?
Advantages, biological facts and environmental impact
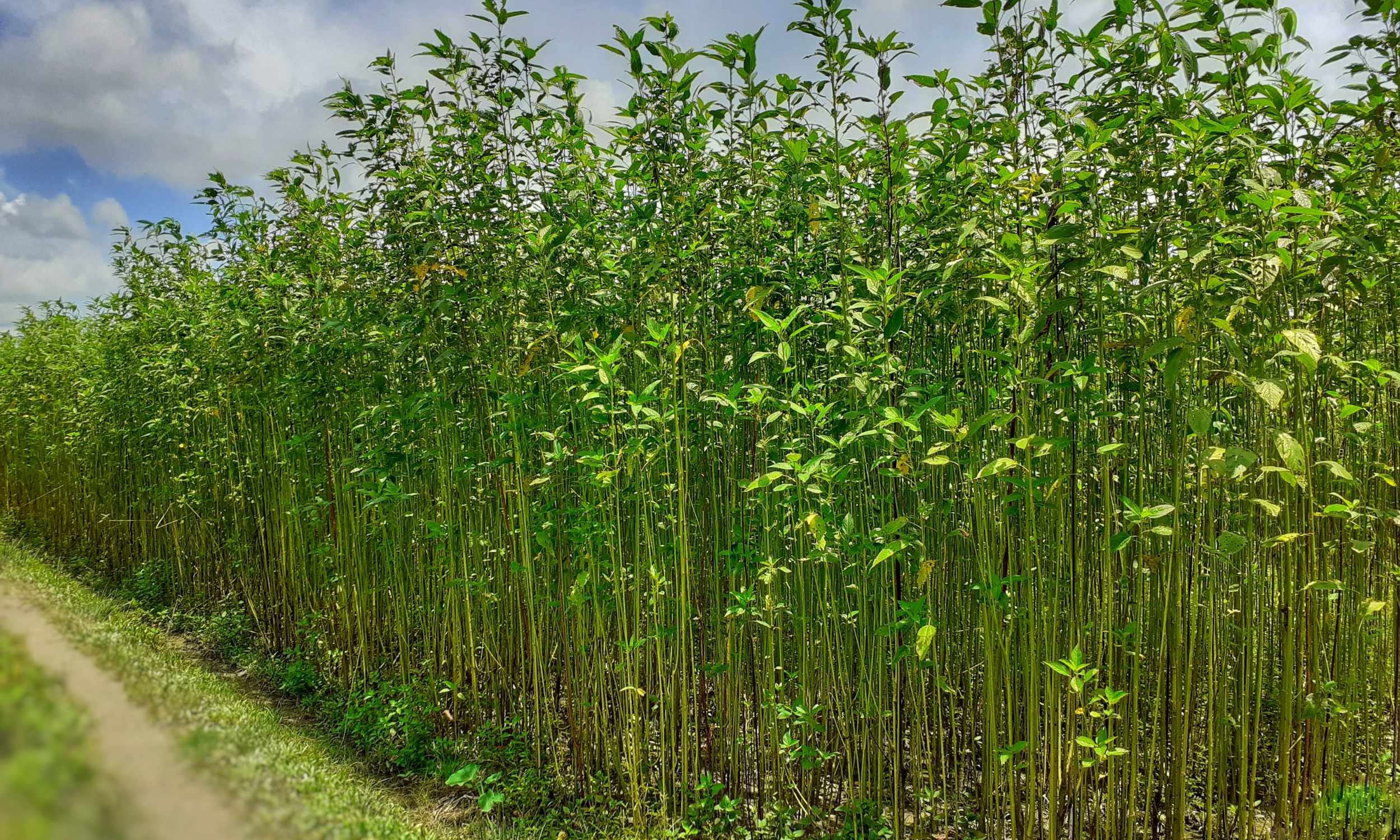
Jute - a lot more than just fiber
From a tying perspective, jute rope is lighter and much easier to work with. It has very low elasticity, making it the optimum for safely suspending.
Without fibre dust and any additives, jute has the lowest known incidence of allergy. Its texture permits strong, secure knots, lashings and bindings that can be reopened multiple times. It doesn’t pick up dirt like hemp and linen, that can quickly feel sticky. Without additives, it has no smell, and with use, its lustre begins to golden beautifully.
But there are also environmental reasons. Jute is biodegradable and thus doesn’t cause any pollution during disposal. It uses biological, rather than chemical fertilizers, pesticides and weed killers/fungicides. It can be batched and coated using plant–based oils and starches.
Biological efficiency is much higher than wood as jute is a fast–growing annual crop taking only 4–5 months to maturity. Production waste is biodegradable and used as manure.
Jute plants purify the air and have a carbon dioxide absorption power many times higher than trees. In the growing period, one hectare of jute plants will absorb around 15 billion kilograms of CO2 and liberate 11 billion of oxygen.
Jute products require only 7% of the energy required for the production of synthetic counterparts. Total energy consumption during jute agriculture and jute production is only 10 gigajoules per tonne.
Jute is a natural fibre and an annually renewable resource. It has high biomass production per unit land area. Leaf and crop waste left in the field is transformed into organic materials, reducing demand for supplementary fertilizers. Jute is proven to be absolutely harmless in terms of global warming.
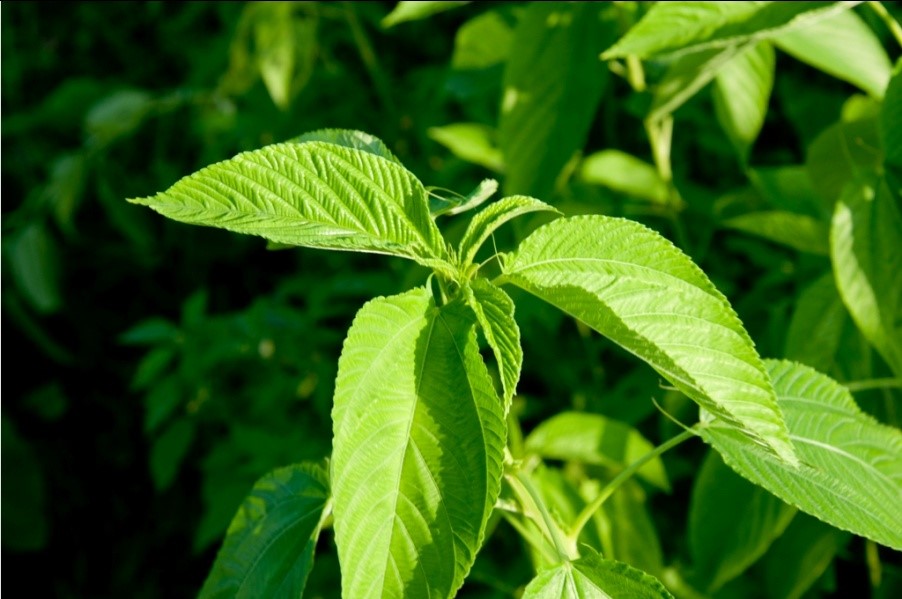
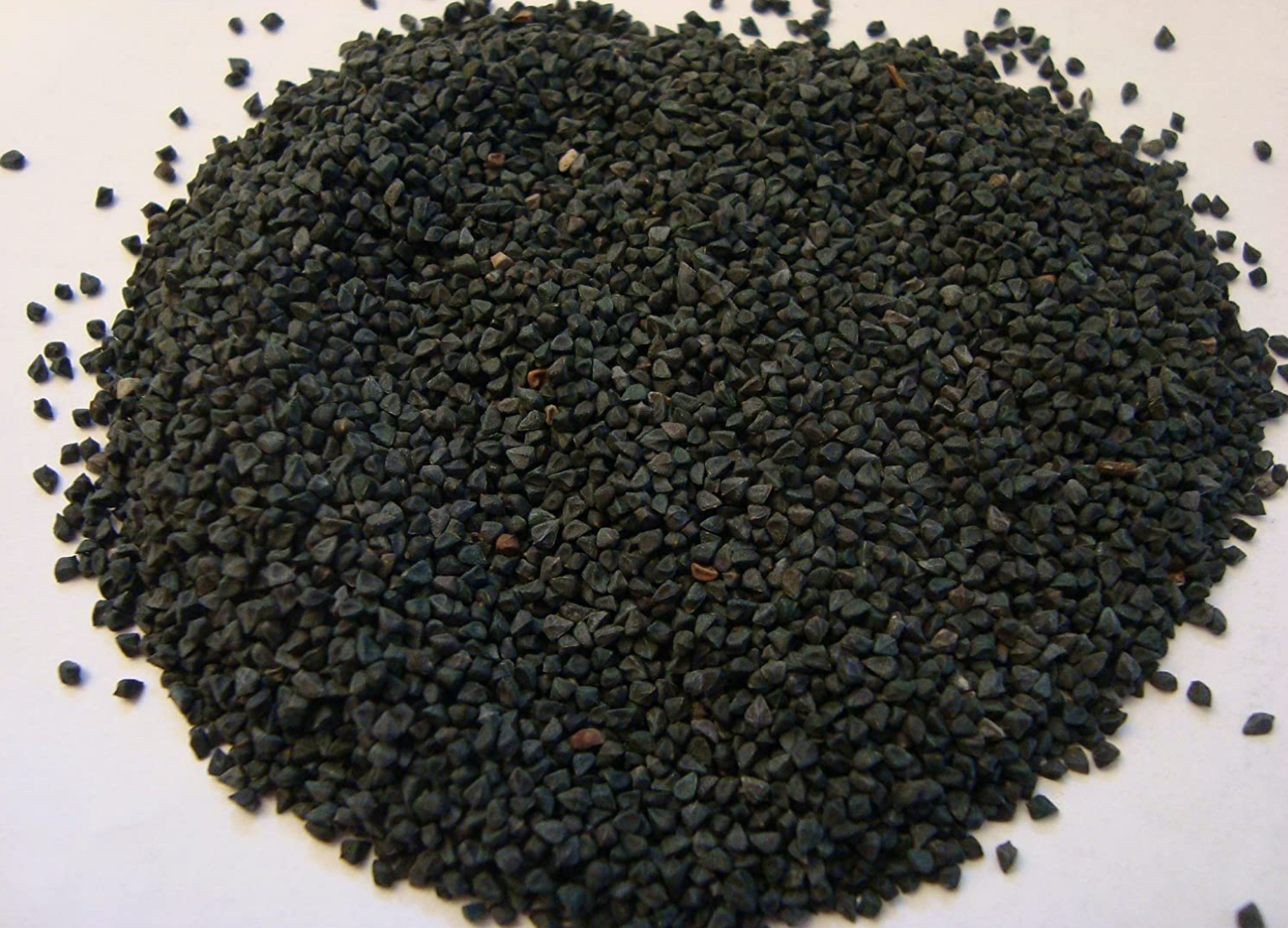
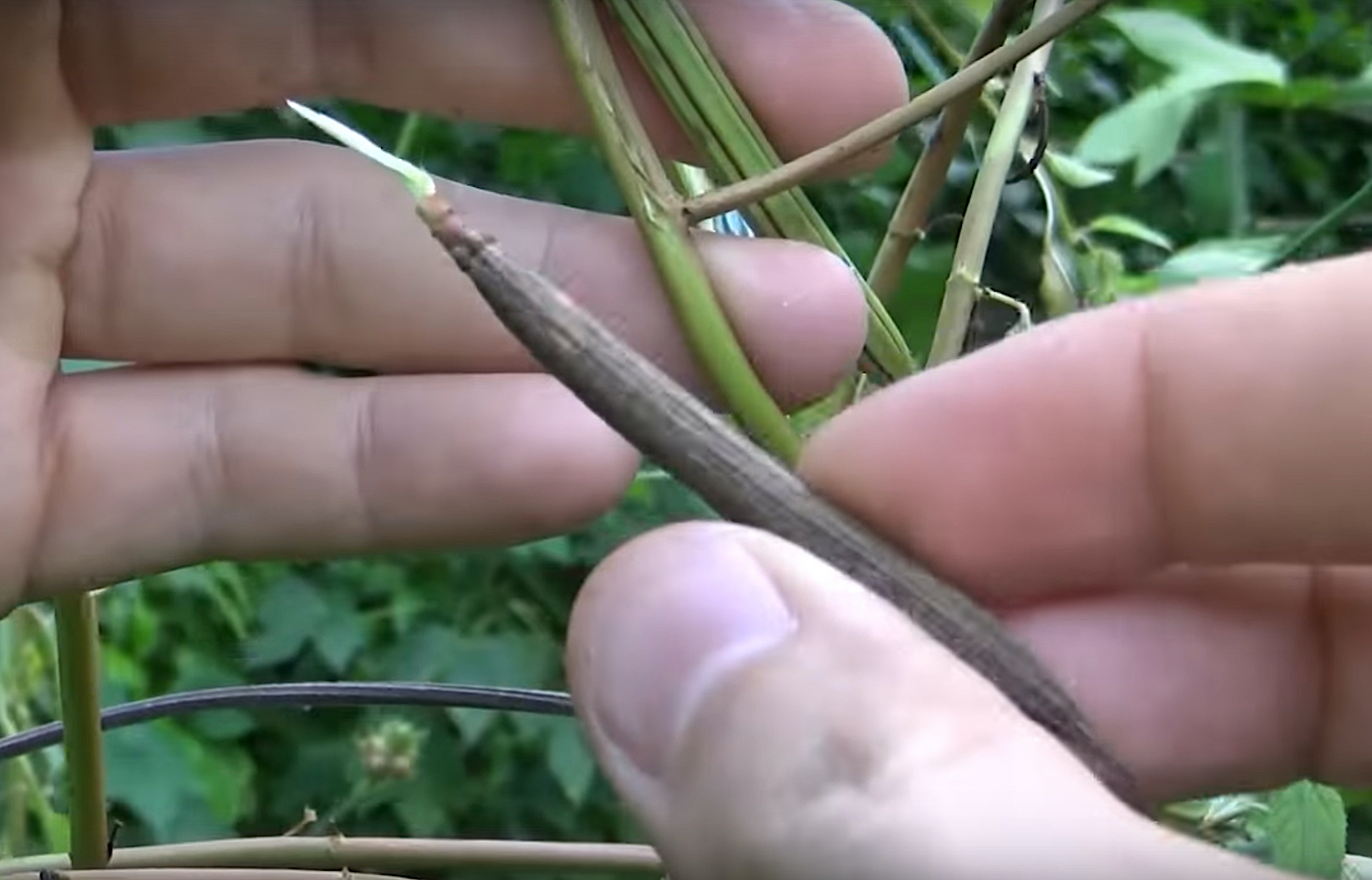
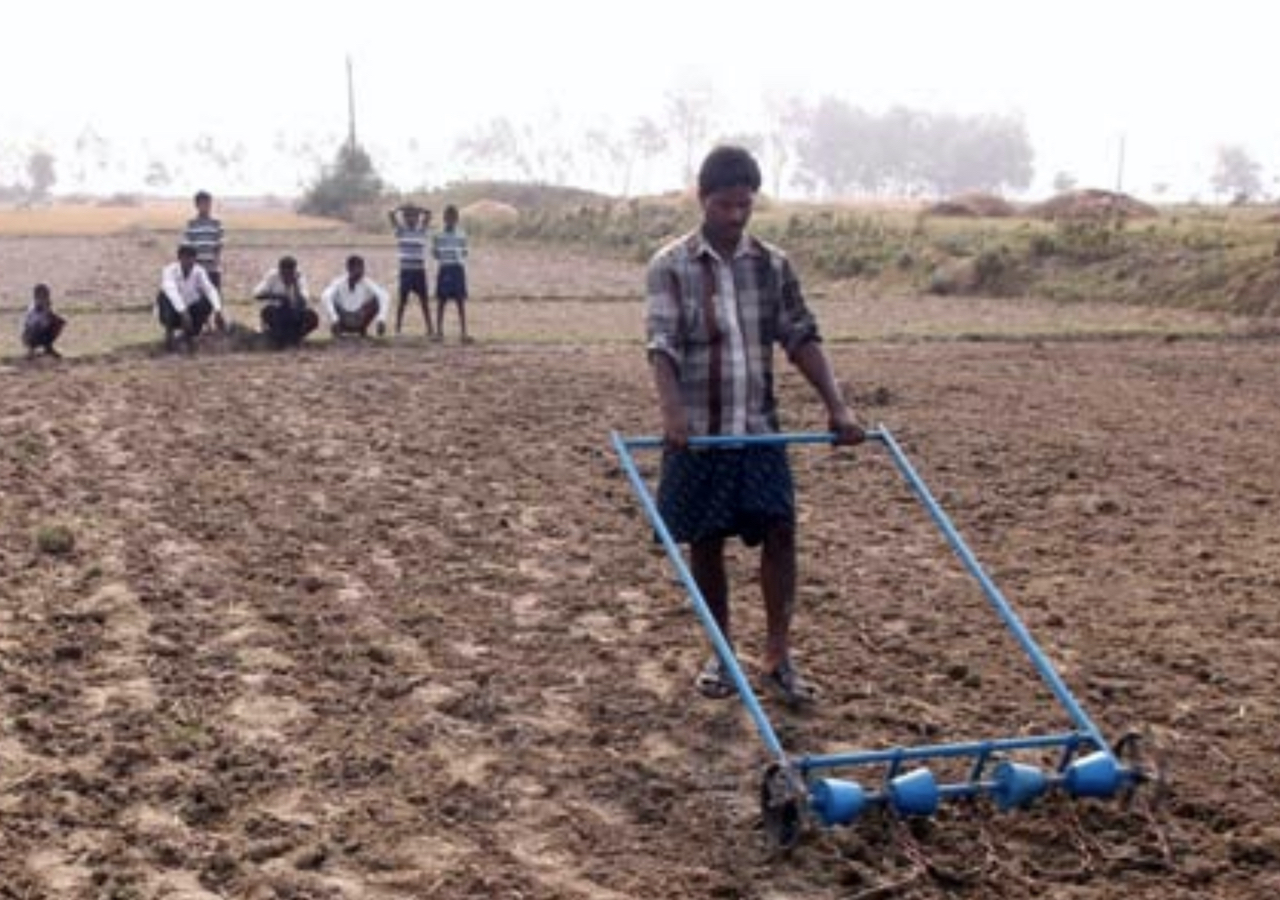